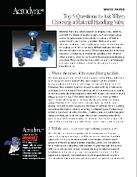
An international EPC provider contacted Aerodyne recently for new rotary valves for a customized smelting process. The company needed roughly 17 rotary valves to handle arsenic dust from a feeder. The temperature of the application ranged from 5°C to 45°C. Originally, the facility contacted Aerodyne about purchasing the rotary H valves. However, after working through the specs of the application, the Aerodyne salesmen suggested the company try using the Vacu-Valve trickle valve system in place of the rotary valves.
The open-construction Platypus and the closed-construction Armadillo trickle valves are the most economical ways to manage dust discharged from bag filters or cyclones under negative pressure. The fitted duckbill sleeve adjusts to the desired vacuum and material is continuously discharged. It requires no controls, lubrication or power supply and easily handles abrasive materials. This trickle valve can be used in higher temperature applications as well. The Vacu-Valve® dust discharge trickle valve is available at a fraction of the cost of the rotary airlock valves it replaces. Additionally, there are multiple duck bill sleeve options available to better suit a wide variety of applications. The Vacu-Valve is extremely cost-effective and was nearly 1/5 the cost of what the company would have spent on rotary valves.
For more information on this cost-effective solution to rotary valves, click the photo below.