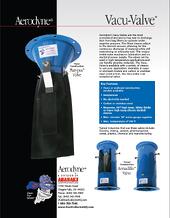
An OH steel manufacturer was having issues with its old trickle valve. The company has 16 shaker baghouses on a hot metal reline station at its plant. When the steel is being made, the molten contents are poured into massive ladles. The ladles are vented and the gas is sent to the shaker baghouses. As the gas cools, steel particulates in the gas stream solidify and are dropped from the baghouse into a trickle valve system. The trickle valve system collects and funnels all of the dust particulate for easy removal from the plant. However, the plant’s trickle valve was quite old and was not operating as it should. The facility reached out to Aerodyne and inquired about the Vacu-Valve Trickle Valve System as a replacement.
After speaking with an Aerodyne salesperson, the company purchased an Armadillo Vacu-Valve with special transitional pieces. The closed-construction of the Armadillo Vacu-Valve trickle valve is most economical ways to manage dust discharged from bag filters or cyclones under negative pressure. The fitted duckbill sleeve adjusts to the desired vacuum and material is continuously discharged. It requires no controls, lubrication, or power supply and easily handles abrasive materials. This trickle valve can be used in higher temperature applications as well. The Vacu-Valve dust discharge trickle valve is available at a fraction of the cost of the rotary airlock valves it replaces.
See an animated demo and get more information on the Armadillo or Platypus Vacu-Valve trickle valve system by clicking the photo below!