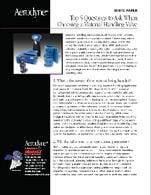
A manufacturing company in Michigan that specializes in glass and other building materials for commercial, residential, and the automotive industries was experiencing numerous problems with its glass dust collection system’s rotary valves. The facility uses 10 cartridge collectors that are fixed with rotary valves. The particulate being fed through the system is a sand and limestone mixture. Both the cartridge collectors and the rotary valves were constantly getting clogged with the dust and the time and money that was being wasted on cleaning, maintenance, and replacement of parts became too much for the facility to handle. Hoping there was a solution to the problem, the plant manager reached out to Dan Navicky at Aerodyne Environmental.
After going through the specs of the operation, Dan suggested the facility try using the Vacu-Valve Trickle Valve System to replace the existing rotary valves. Trickle valves are the most economical way to manage dust discharged from bag filters or cyclones under negative pressure. The fitted duckbill sleeve adjusts to the desired vacuum and material is continuously discharged. It requires no controls, lubrication or power supply and easily handles abrasive materials. This trickle valve can be used in higher temperature applications as well. By placing a Vacu-Valve fitted with a Neoprene sleeve at each of the cartridge collectors, the facility was able to eliminate the glass dust removal issues and help to prolong the cartridge life.
Is your glass dust application experiencing problems due to clogged collectors and faulty valves? The Vacu-Valve is your cost-effective, low-maintenance solution. For detailed literature, animated demos, and application literature on the Vacu-Valve, click the photo below.